Benefits Of Collaborative Robots [Complete Guide]
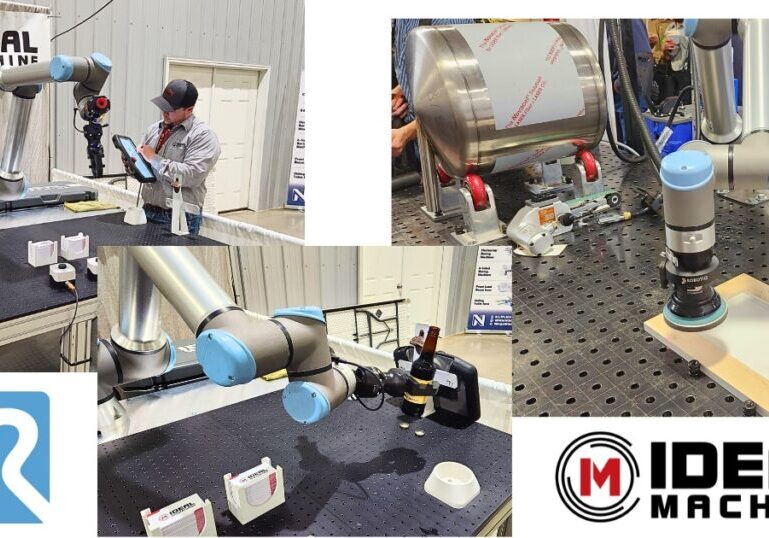
Benefits Of Industrial Collaborative Robots
Let’s talk about the benefits of collaborative robots. Robots, specifically collaborative robots can change the way your manufacturing company operates. They save you time and money on labor costs as well as increase efficiency and product consistency.
When you invest in a collaborative robot arm you are freeing up your employees to do more important, skilled tasks. These are just some of the many benefits of utilizing collaborative robots for repetitive tasks that otherwise your employees would get tired of. Collaborative robot arms provide a tireless level of reliable task completion that a human being isn’t capable of for hours on end.
What Is A Collaborative Robot?
The question is, what is a collaborative robot? A collaborative robot, or cobot for short, is a specially designed robot arm that is safe for human operators to work with. Large-scale industrial robots for manufacturing can be dangerous for people to work alongside because they don’t have the same human-friendly safety features as collaborative robots.
Collaborative robots are equipped with special sensors that immediately halt them in the middle of their functions when they meet very low levels of resistance in their operating paths. This means that if a human operator accidentally bumps your cobot or gets in the way of its operating path it will stop immediately, preventing the injury of your employee or the damage of your product. This makes collaborative robots ideal for small and medium-sized manufacturing companies.
Collaborative Robot Definition [Cooperative Robots]
Collaborative robots have been called cooperative robots. This is a great way to think about collaborative robots because they have been designed to “cooperate” safely with human operators. Cooperative robots are a safe and effective way to scale up your manufacturing tasks while keeping your employees safe. Cooperative Robots can take over the repetitive, menial tasks that don’t require higher levels of problem-solving. By using cobots, you can free up your employees to do more fulfilling tasks that require attention to detail and complex steps.
Cobots Vs Robots
Let’s talk about cobots vs robots quickly. It’s important to understand the stark differences between cobots and traditional industrial robots. Although they can be programmed to perform the same kinds of tasks like welding, palletizing, or basic assembly functions they are very different. Cobots, or collaborative robots, are designed to be safe for employees to work with. They are lighter weight, made with rounded edges, and feature built-in safety features that prevent them from injuring your employees. In contrast, industrial robots are bigger, and heavier, and do not have the same human-friendly safety features.
4 Collaborative Robot Arm Functions
There are many different collaborative robot functions to help with different production and manufacturing tasks. As we go through these common uses you will begin to see all the benefits of collaborative robots. We’re going highlight 4 of the most common cobot functions we see businesses taking advantage of, cobot welding, cobot sanding, cobot palletizing, and cobot pick and place functions with end-of-arm tooling grippers.
Collaborative Welding Robot
Collaborative welding robots are a very common way people are utilizing cobots. Having a cobot weld for you is a great way to speed up production and reduce mistakes. If you have identical parts that you manufacture on a regular basis then automating your repetitive welding is a great way to speed up production.
Collaborative Robot Sanding Arms
Woodworking sanding functions are another great utilization for cobots. Implementing a collaborative robot sanding arm could be a useful solution for your manufacturing if you operate in the woodworking space. Repetitive sanding tasks can be easily programmed creating a cobot sanding arm that never gets tired and never changes in quality of its programmed pathways. Robot polishing is a very comparable function to robot sanding. Check out how we’re using a robot polishing arm in our manufacturing shop.
Collaborative Robot Palletizer
Collaborative Robot Palletizers are another common manufacturing application. For companies that want palletizing solutions to increase their production efficiency and cut labor costs a collaborative robot is a solution worth considering. Robot palletizing can free up your employees to handle more complex and important decision-making tasks while your robot arm handles the stacking and wrapping of palletized products.
Collaborative Robot Grippers & End Effectors
There are so many different Collaborative Robot Grippers and End-Effectors that you can accomplish virtually any manufacturing task. End-of-arm tooling for cobot arms offers you all sorts of solutions to material production from sanding to welding to pick-and-place to palletizing. Based on the functions or tasks you want a collaborative robot to perform you can go with robot grippers that articulate like human hands or choose end effectors like different sanders to sand cabinet doors or drawer boxes. You can go with manual tool changers or opt for robot-programmed tool changers for a completely hands-off approach.
Integrating Collaborative Robots Into Your Manufacturing Process
Integrating Collaborative Robots into your manufacturing process may seem like a good idea but there are many factors to consider. Cobots are a long-term investment and aren’t right for everyone. Trying to decide when to integrate a collaborative robot can feel like an overwhelming decision. Here’s our list of factors to help you decide if it’s time to consider integrating a cobot into your manufacturing.
Repetitive Tasks
Do you have repetitive, repeatable tasks in your manufacturing process that need to be accomplished day in and day out? A repetitive task that never changes but always needs to be completed can be a great thing to automate with a cobot.
Optimizable Functions
Do you have a production step that could be optimized and made more efficient and reliable with a robot? A good example would be cabinet door sanding. If you rely on your employees to sand cabinet doors all day long you know that there are inconsistencies over the course of the day. Arms and shoulders get tired, your employee’s hands cramp up, maybe they lose focus on the task itself due to its repetitive nature. A robot doesn’t have those problems. In this sanding example, your robot would produce perfectly consistent cabinet doors all day. It will apply exactly the same pressure while sanding each door. You can set up a collaborative robot sanding cell to sand multiple doors in a sequence. All your operator will have to do is load and unload doors as your robot sands them and perform routine quality checks.
Adequate Volume
In order for a collaborative robot integration to make sense you need to have adequate volume demand for your business. If you only deal in custom, one-off projects then a cobot may not be the best fit for your business. If you make a product or products that are mass-produced regularly and you would benefit from more parts manufactured faster then considering a collaborative robot could be beneficial.
Wrapping Up The Benefits Of Collaborative Robots
Collaborative Robots for Manufacturing offer many benefits. We’ve touched on some of the key benefits that collaborative robots offer to companies looking to scale their production. Cobots will help you to improve the quality of your products, increase your material throughput, cut down on your production costs, and free your employees for more important, problem-solving tasks.
Robots aren’t for everyone and that’s ok but for the right companies they can revolutionize manufacturing. If you’re interested in learning more about collaborative robots and how they could benefit you contact us today to start a conversation. Ideal Machine became a Universal Robots Certified Integrator in 2023 so that we can provide collaborative robot education and help manufacturers create robot solutions for their production.